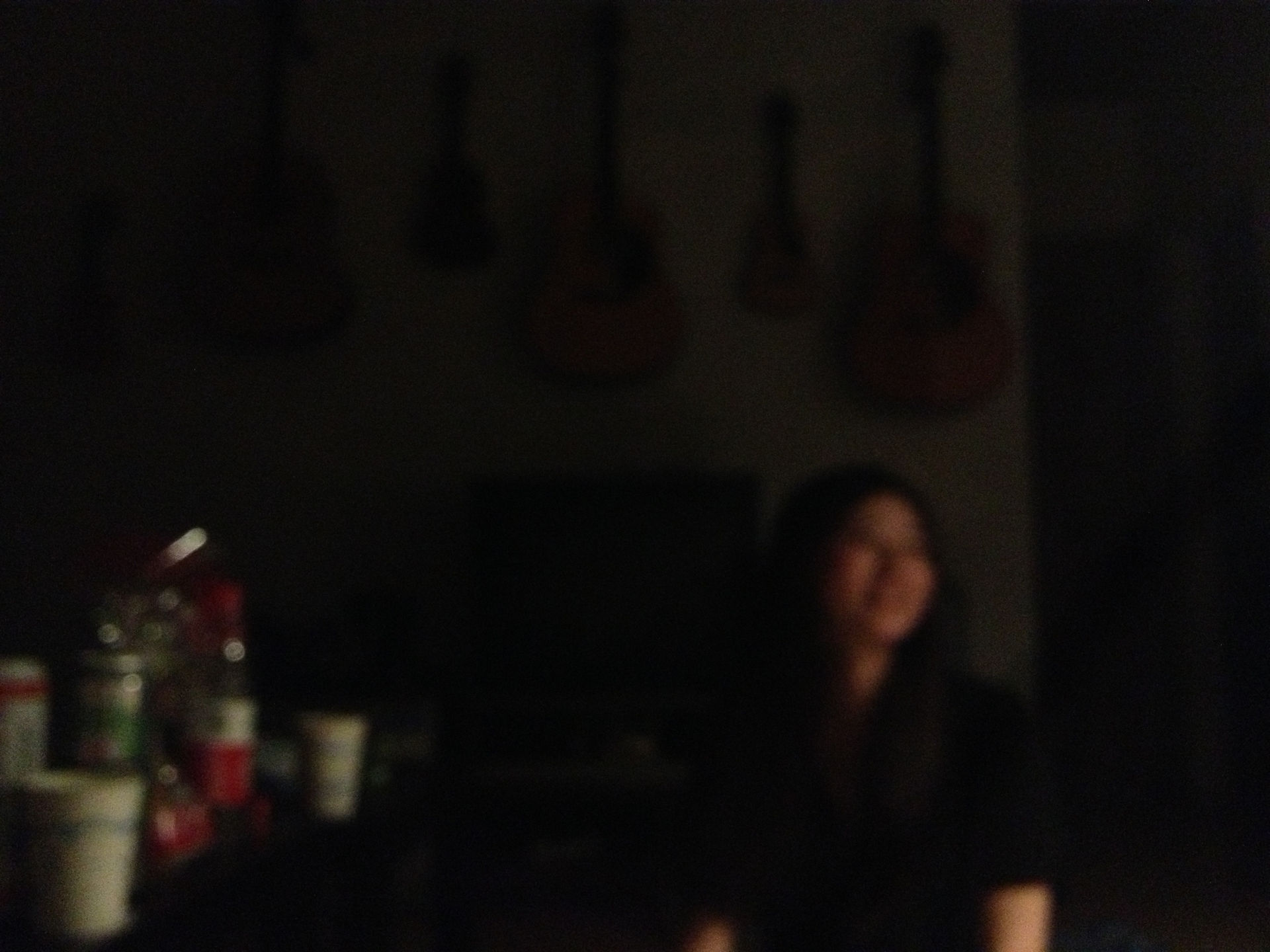
DFE PROJECT -- EWB BOTTLE CUTTING MACHINE DESIGN
VIEW FULL REPORT
OVERVIEW
Team Project
Design for Environment
Carnegie Mellon Univerisity
Pittsburgh, PA
November - December 2015
MY ROLE
Research | Conceptual Design | Conceptual Sketch | Prototyping | Final Report (Design Concept and Conclusion part) | Final Presentation
SKILLS
DFE Principles | DFA Principles | Laser Cutting | Inventor

THE CHALLENGE
Our team was partnering with Engineer's Without Borders (EWB) to create synthetic roofing thatch for houses in Vietnam by reusing empty 2L plastic bottles. We chose to focus on designing a machine which can cut bottles into uniform 2" strips in an efficient way.
Several design constraints were communicated from the EWB team.
1. The machine should aim to process 1 bottle per second and cost under $500.
2. The machine should be semi-automated and use no more than two people to operate it.
3. The plastic bottle inputs are likely to vary in shape.
A GLIMPSE OF THE FINAL DESIGN
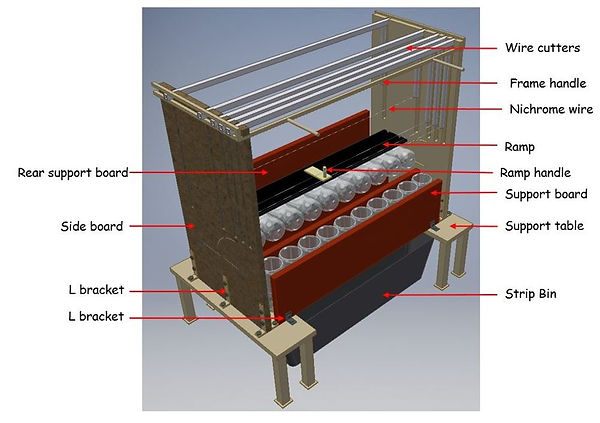
IDEA GENERATION
Our team began brainstorming for the automatic ways of cutting bottles and we thought of 4 ways of cutting bottles into strips including water jet, laser cutter, hot wire and blades. And we came up with several totally different design concepts.



CONCEPT SKETCHES
We have thought about a variety of machines using blades or hot wires. The first design considered using blades since they produced a faster production rate. It was discarded due to the high cost of purchasing 7 blades. The second design reduced the number of blades to 5 at a cost of a lower production rate and a larger amount of space.
The final two conceptual designs were made using wire cutters as the primary cutting mechanism. Although the idea of an adjustable box was highly appealing since it can hold a large capacity, solving the interference with the wires was difficult. Therefore, the idea was modified to generate our final design.
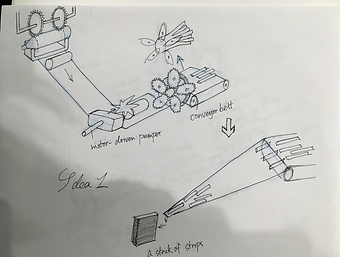

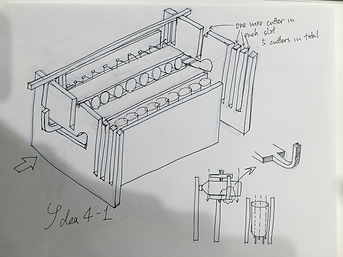
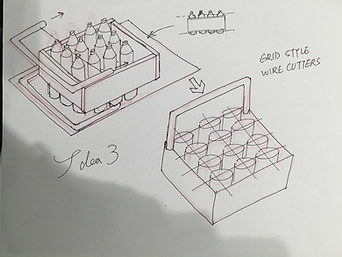
PROTOTYPE AND VALIDATION
The most crucial element of the cutting machine design is the hot wires used to cut the bottles into strips. To verify that hot wires are physically possible to cut through the bottles as well as to determine the cutting speed, our team used a 20W Manix hot wire foam cutter obtained from the fine arts wood shop at Carnegie Mellon University for testing.
We also cut a bottle with a band saw and compared the two strips cut by different tools. There was a noticeably jagged edge to the plastic strips cut with a band saw.

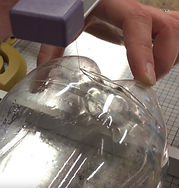

FINAL PRODUCT
Our team proposed a machine that costs 40% less than the proposed budget at $277 that is capable of processing 1 bottle per 6 seconds while only requiring 325W of power. Moreover, manufacturing the machine generates a small carbon footprint of 144.4 lbs.
The final design uses five nichrome hot wire cutters in total with two designated to cut the tops and bottoms off and the last three to cut the bottles into uniform 2” strips. Only one person is needed to operate the machine. Uniform movement of the wire cutters enables twenty bottles to be processed in the machine at a time.
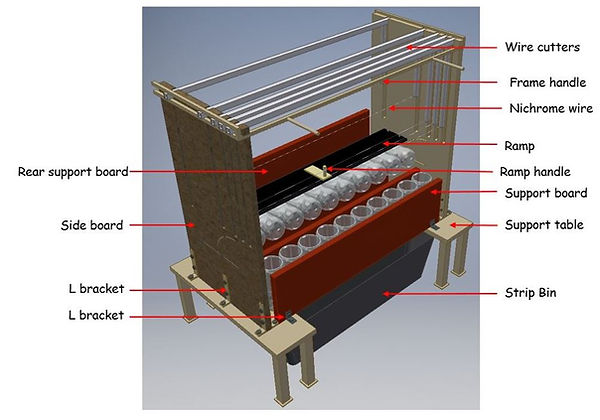
USER INSTRUCTIONS

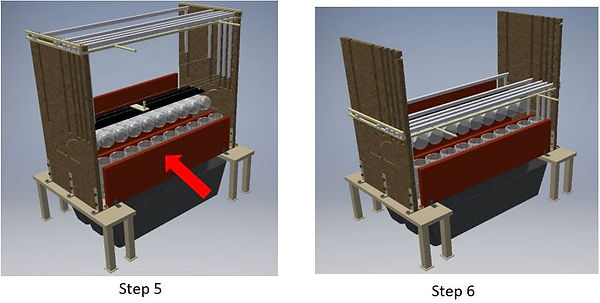