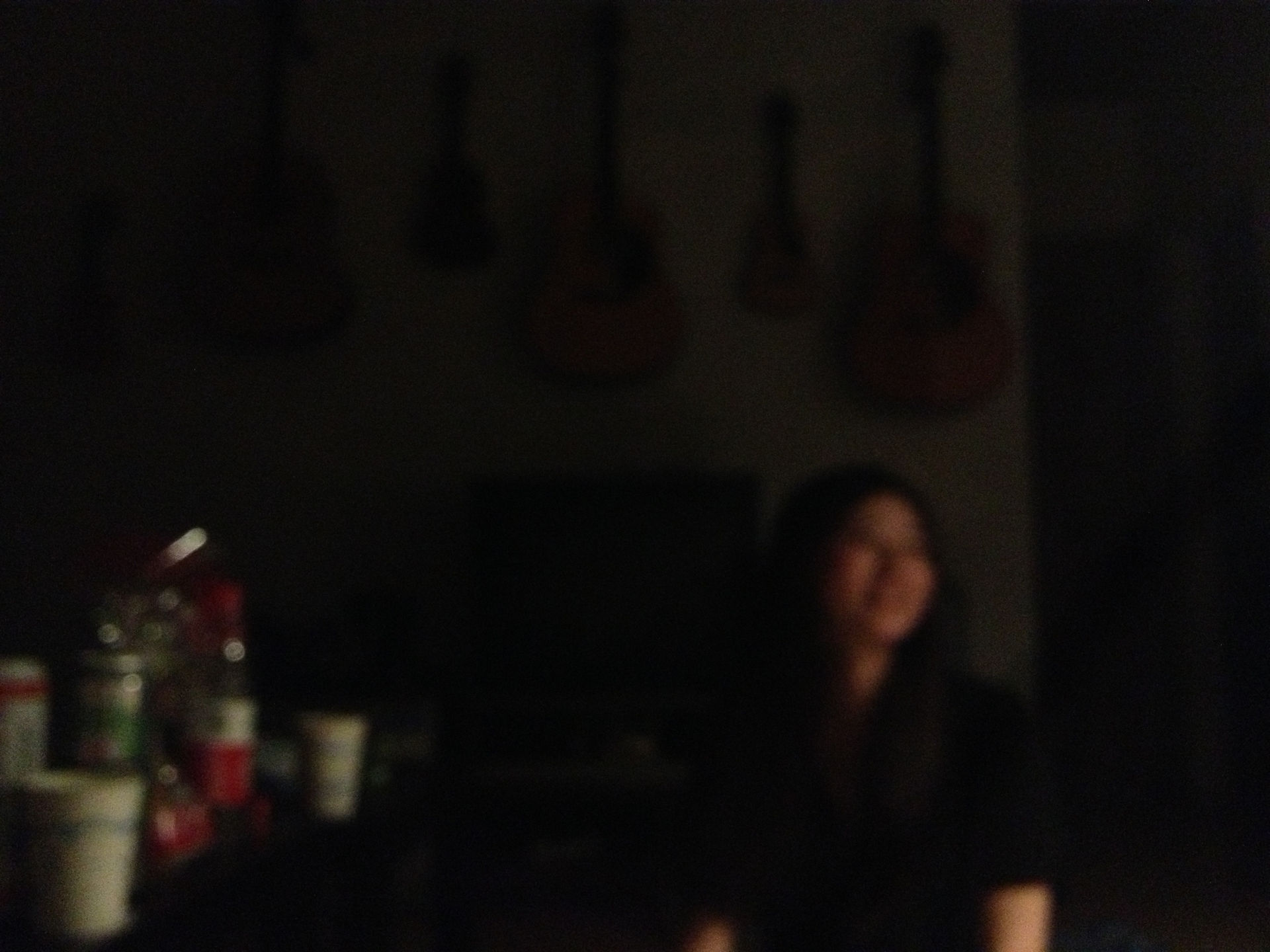
PORTABLE CHARGER DESIGN
VIEW FULL SLIDES
OVERVIEW
Individual Project
Freelance Work
Pittsburgh, PA
April 20-27, 2017
MY ROLE
Research | Conceptual Design | Embodiment Design | Prototyping | Final Presentation
SKILLS
DFE Principles | DFMA Principles | Material Selection | Solidworks | FMEA | 3D Printing

THE CHALLENGE
From the user research I conducted, I found that one of the properties people aren't satisfied with is the bulkiness of the current product. They are either too big to fit in pockets, or too heavy to carry around, and thus they are not that 'portable'.
Most people only use portable chargers during travel. As the batteries of smartphones nowadays last longer and longer, I feel it would be enough if a portable charger's full capacity can charge a phone twice.
In my design, My top priority is to make the product impact and light and easy to carry.
A GLIMPSE OF THE FINAL DESIGN
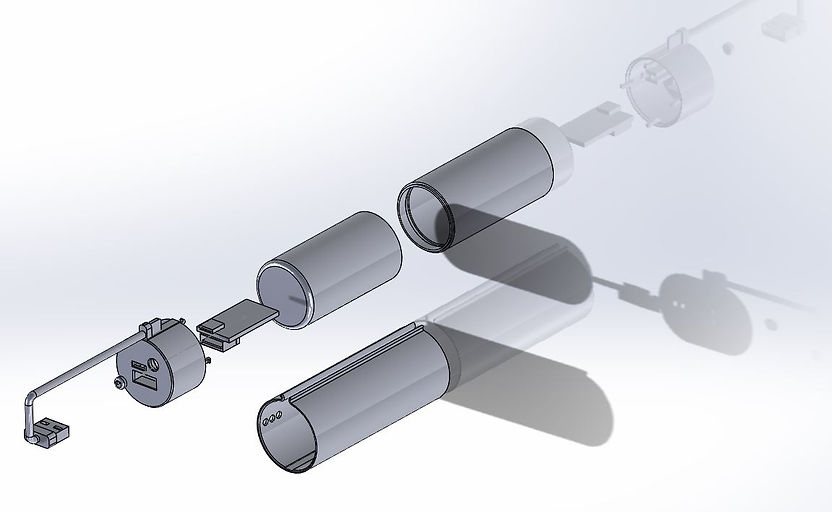
IDEA GENERATION
Three different ideas.


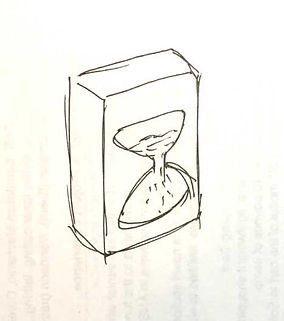
MATERIAL AND MANUFACTURING PROCESS SELECTION
I used Ashby Methodoloty to select the material for the casing and the sleeve. The final choice for casing is PC+PBT blended material, and for sleeve is PVC-elastomer. Please refer to my full presentation on the top right corner if you are interested in the calculation and full details for the method I used.
Since it's a mass produced consumer goods, it makes sense to use injection molding as manufacturing process.
FINAL PRODUCT
Now I present the final product as below.
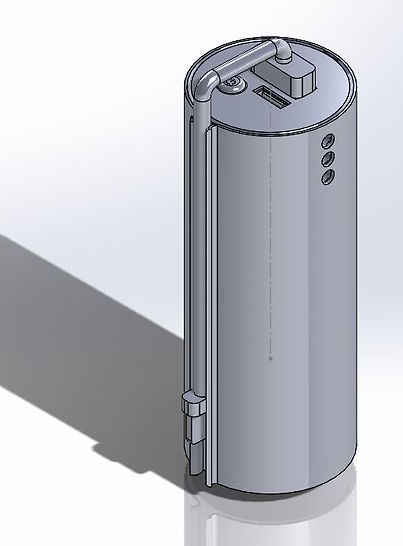
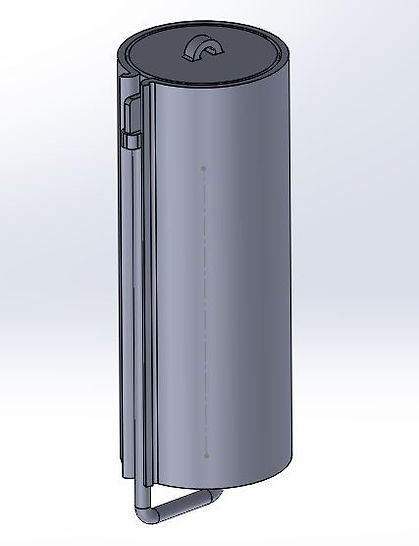



DFMA & DFE PRINCIPLES APPLIED
-
Reduce the total number of parts
-
Use of standard/ commercially available components
-
Design parts to be multi-functional
-
Design parts with tolerances within process capability: no extremely tight tolerances
-
Eliminate surface-finish operations
-
Avoid separate fasteners
-
Design the product to be foolproof during assembly: components should be designed so they can be assembled only one way.
-
Design for ease of assembly: chamfers, tapers should be designed on mating parts
-
Instructions and warnings can be molded into the base of the charger to replace the traditional sticker
-
Avoid or minimize use of hazardous and toxic materials
-
Use materials which are renewable and recyclable
-
Minimize use of thermosets
-
Minimize the number of materials used
-
Transport by ship or train instead of plane and lorry
-
Design for easy maintenance and repair
PROTOTYPE AND VALIDATION
3D printed the casing and sleeve as they are the part will be actually manufactured.